We live in an era characterised by the energy crisis and the need to reduce the carbon impact caused by human activities. The increase in production activities and industrialisation in urban environments is generating a higher demand for energy and technological advancements that offer new, more efficient, and low-energy consumption solutions are not sufficient to reduce the concentration of greenhouse gases in the atmosphere. In this context, waste plays a key role in containing and reducing rising ground temperatures.
Paper mills are also considered high-impact activities in the carbon cycle, and compensating for these emissions by purchasing carbon credits on the mandatory market is not enough, neither for climate commitment nor for environmental sustainability, a concept widely promoted in corporates marketing slogans today.
We need to do more. It is necessary to analyse all industrial processes and reinvent them to reduce operating costs and waste, exploring possible new paths towards a circular economy.
An “end of waste” process is defined as a production cycle that “transforms” waste into a product or, to some extent, as stated by the European Directive 2008/98/EC, into a by-product. These processes, often experimental, do not always reveal how much residual reject remains at the end of the treatment and whether the level of processing achieved offers an acceptable economic advantage. This acceptance of partial results, if sufficient for the paper mill, is certainly not acceptable for the environment. In the perspective of a true circular economy, further efforts are needed to create virtuous cycles even in the medium to long term.
In summary, extracting lightweight plastics from the pulper waste, in a percentage sufficient to achieve a positive economic advantage, is no longer acceptable. Respecting the environment is no longer an option! We no longer have time to procrastinate. ECUBE‘s experience in treating pulper scrap at a paper mill dates to 2020 when, during the COVID-19 pandemic, an innovative plant for pulper waste treatment was installed. After three years of experimentation and attempts to extract lightweight plastics such as PE and PP, the technical team managed to define a processing protocol and achieve a process that recycles 100% of the pulper waste.
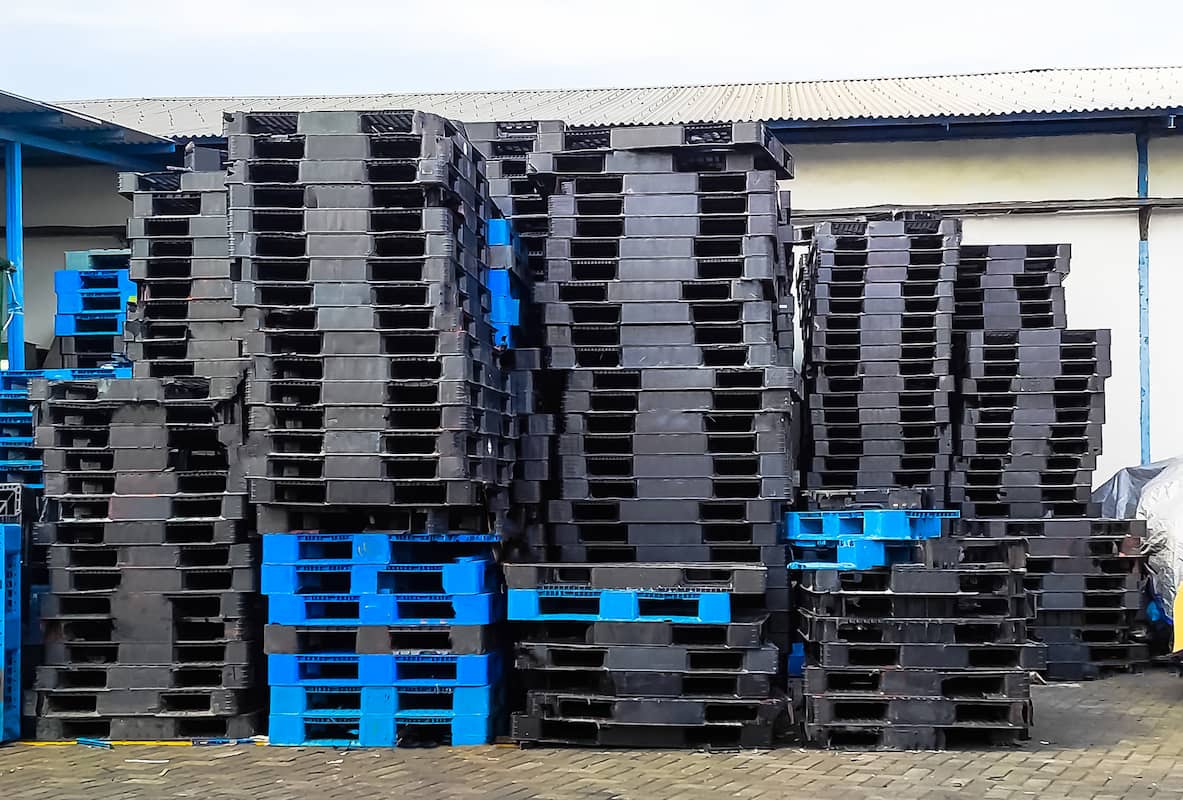
The first phase of pulper pre-treatment includes grinding, separation of ferrous metals, and washing to remove the paper fibre present in the waste. The paper fibre, along with most of the moisture, returns to the paper mill to be further used in the pulping process. The experience shows that the level of paper fibre recovered in the paper mill process transforms into paper pulp between 80% and 90%.
The second, more complex, stage involves further reducing the lightweight fraction through a second washing process to obtain a material free from residual fibre. At this point, a homogeneous material with dimensions smaller than 40 mm is obtained, depending on the grinding mill’s sieve. The material mainly consists of PE-PP-PVC plastics, wood fragments, rubber, expanded polystyrene, and coupled aluminium. There are, in fact, other materials as well, but their quantities are insignificant for the process.
At this stage, the processing phases can take different paths depending on the desired final outcome. The material, as it is, is still considered waste and can be classified under both the EWC191212 and the EWC150102. If necessary, this intermediate material could also fall under the EWC191210, as it can be used as waste fuel for cement kilns or authorized applications. The actual composition of this material is determined by the composition of the incoming mixed paper bales to the pulper and the processing technology adopted by the paper mill.
The residual reject could be disposed of in this form, providing a minimal advantage for the paper mill as it reduces the volumes and disposal costs per ton, as the waste at this stage is more marketable compared to the pulper rejects (EWC030307).
Through energy recovery processes, it is possible to transform this waste into thermal energy within the paper mill, using compact pyrolysis reactors.
One final option for this intermediate material could be the production of plastic pellets, a mixture of PE-PP. Based on the tests conducted on the prototype plant, the average composition consists of 60% HDPE, 2% LDPE, and 38% PP. In this case, the necessary processing steps for the material would involve separating the heavier fraction, such as PVC and traces of aluminium, followed by the separation of undesired lightweight components like wood, rubber, cork, and expanded polystyrene.
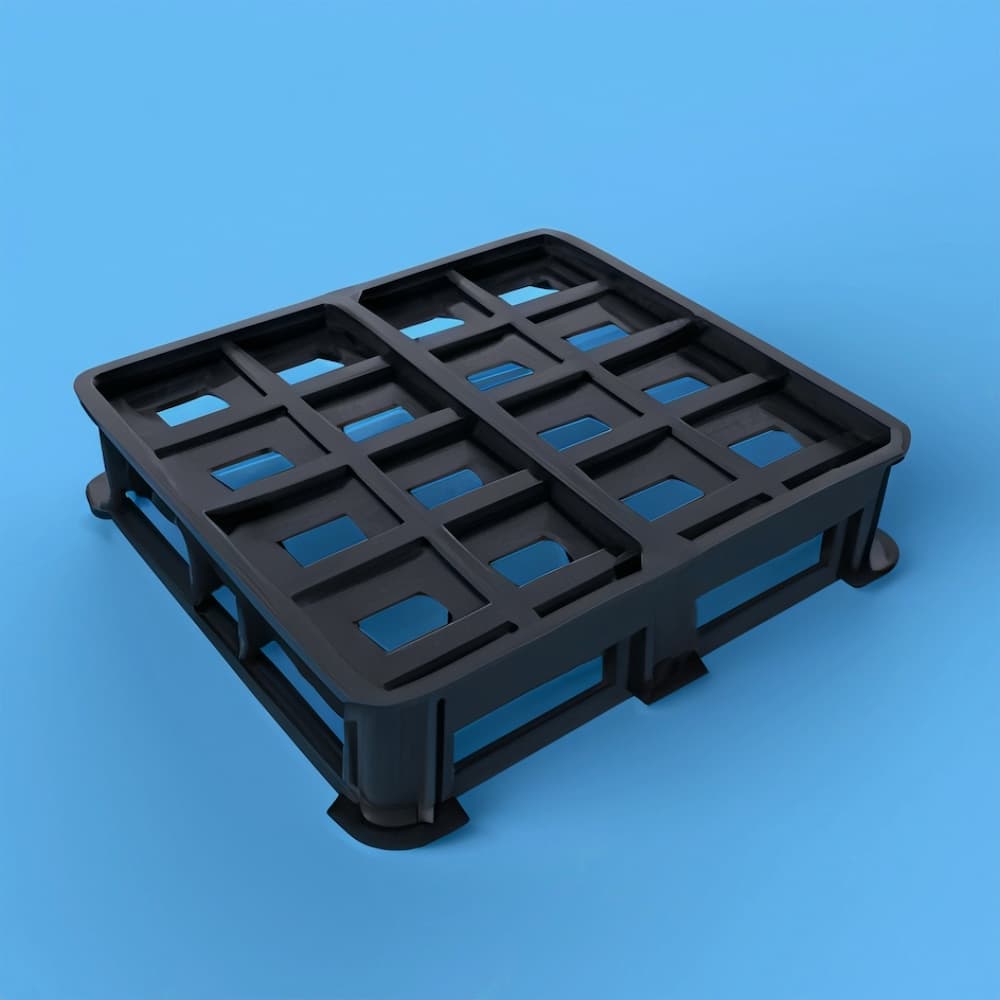
By implementing these processes, a usable and marketable plastic material can be obtained, suitable for extrusion into pellets or for producing PWC (Plastic Wood Composite). However, it should be noted that the higher the purity required for the final product (PE-PP), the greater the waste generated from this additional process.
A different and more challenging option is to create marketable products using all the intermediate waste material. Selling such products also involves researching potential markets and other activities that turn this process into a genuine added business with all its implications.
This plastic material lends itself to many applications, often having solutions right in front of one’s eyes that may be overlooked because of the inertia of always following the same practices. However, I leave it to you, with your ingenuity and creativity, to discover intelligent applications in your working environment.
The paper mill might be interested in a product to be used in the manufacturing process or for handling, such as pallets in many sizes. Currently, most paper mills use wooden pallets in EU standard format of 120x80cm or the 100x100cm format. An external supplier often manages these pallets, responsible for maintaining the pallet fleet’s efficiency and repairing or replacing pallets that are no longer suitable for service.
Exploring the production of plastic pallets or other useful products from the intermediate waste material could not only provide a sustainable alternative, but also potentially save costs and improve overall efficiency for the paper mill. It could also open new revenue streams through the sale of these products to other industries or businesses in need of quality plastic materials for their operations.
The transition from plastic to wood for pallets represents a change in production protocols that requires some variations in processes, but adopting a product derived from an internally produced waste within the paper mill exemplifies a true circular economy.
If you choose to use the lightweight residue from the pulper waste, here are some tips for the implementation. As with all reject treatment processes, the first thing to do is to characterise the available material. Analysing the pulper residue from dozens of paper mills, we have observed a certain uniformity at the source of the waste, but it can vary between mills depending on the different treatments employed to reduce disposal costs.
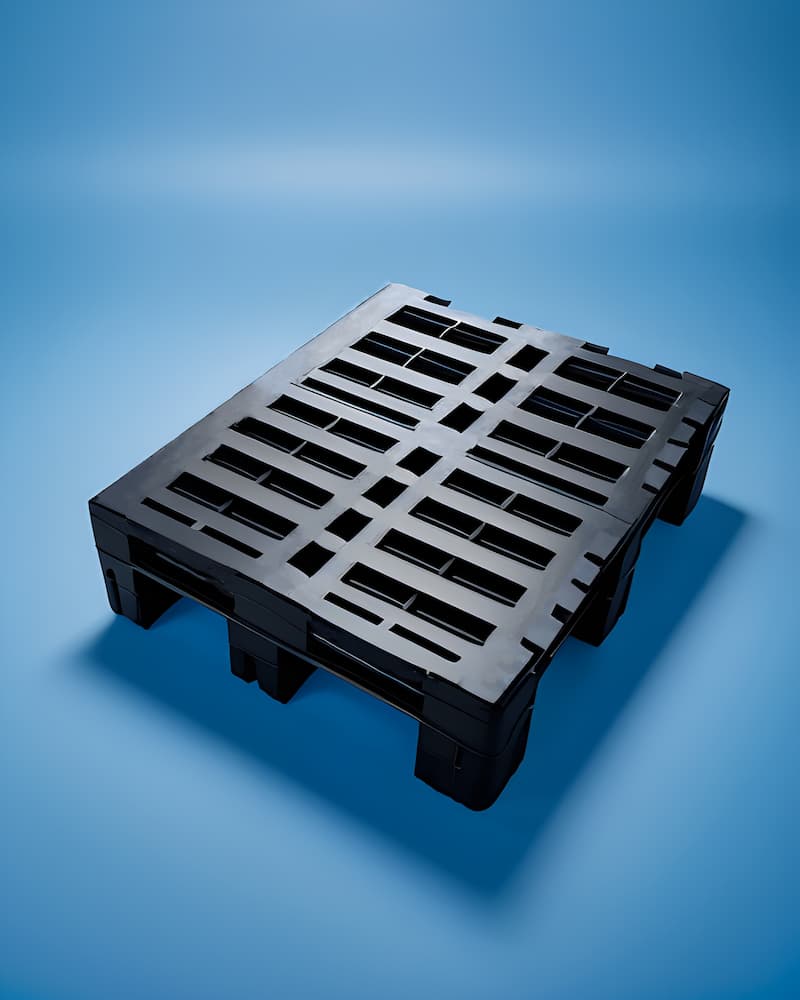
To produce a pallet or any other article using the lightweight fraction of the pulper waste, the following operations are required, assuming there is no need for further separation, and all the lightweight fractions like plastics, wood, and coupled aluminium traces are kept together. The first phase is drying, which can be achieved through centrifugation, reducing the moisture content to below 10%. If a lower moisture level is required, a second pass through the centrifuge or a hot air-drying phase is necessary, which may present some challenges. Following the drying phase, further grinding is performed to ensure product uniformity and prepare it for the moulding process.
The pallets are moulded using standard vertical presses with four columns, employing appropriate techniques available on the market. If higher mechanical characteristics are required, a special additive can be applied to provide superior tensile and compressive strength. These additives can be applied through fully automated robotized spray cells.
As evident from the various processing options, treating pulper waste can be done in different ways and for various purposes. As with all projects, it is advisable to conduct a feasibility study to analyse both the economic and technical aspects within the specific context of the paper mill and then choose the most suitable path according to its needs. This path can be entirely undertaken within the paper mill or by collaborating with a specialised partner who is competent and genuinely interested in achieving results geared towards environmental protection.